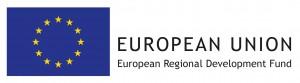


This tender requires a functional specification for the power electronics suitable for use within a subsea pressurised container. A fixed price quote is needed for the upgrades to the current control sytem, assembly, commissioning and testing of the system in the workshop prior to handover.
Scope of Works
Design and Functional Specification
This tender requires the contractor to design, develop, and procure the materials and parts to build a fully functioning subsea power control unit (SPCU). The specification of the electronics system should be suitable for use within a subsea pressurised container required to support the turbines and power conditioning equipment. Furthermore, the SPCU needs to be suitable for connection to national electrical grids in the UK and EU. However, initial sea trials will be connected to an off-grid power dump barge[1].
Requirements:
- The specification of the equipment needs to consider the remote-control aspects of this system being submerged up to 20m below the surface and all the possible faults that could occur during operation along with mitigations and control aspects required for continuous and reliable operation.
- The SPCU needs to have very high availability and hence some degree of redundancy to allow operation to continue despite a fault or “graceful degradation”. There is an opportunity to reduce the specification after the initial SPCU is built and tested before full integration and deployment at sea. When the system dynamics and thermal signatures and faults/failures are better understood there will be a clear path to cost reduction.
- Within the specification of the equipment, the contractor needs to provide the thermal outputs of each main component and the ideal environmental operating conditions for maximum efficiency and understand the loses in efficiency resulting from that component.
- The contractor should integrate the heat exchanger linked to a keel cooler located on the exterior of the SPCU pressure hull. QED will provide the necessary penetrations for the water cooled system.
- Define the specification and space requirements for a Subsea Transformer Unit (STXU) along with the cabling and connector requirements for exporting the power.
- There is a low level power requirement for the tidal turbines to operate the instrumentation sensors on-board the turbines alongside the HPU for the brakes. This 3-phase 400V can be taken from the export cable either supplied from the grid or parasitic power drawn from the power generated by the turbines. However, a backup system potentially run by battery / inverter may be useful.
- Added value further down the line would be provided by the use of sensor-less control of the turbine removing the requirement for an encoder from each turbine. This is quite a temperamental system which often generates as many faults as it detects. It also complicates the internal castings making them expensive components to manufacture.
[1] There is a potential issue here mainly around synchronisation with the grid, a grid tied inverter uses the grid as a voltage, frequency, and phase reference (essentially frequency matching). If you won’t have a grid connected to the back end of the inverter(s) then you either need an off-grid type inverter (which will generate its own voltage and frequency) or a system on the barge that emulates the grid. It would be easier and cheaper to use an off grid, or even a hybrid inverter, which would allow operation in both ‘modes’.
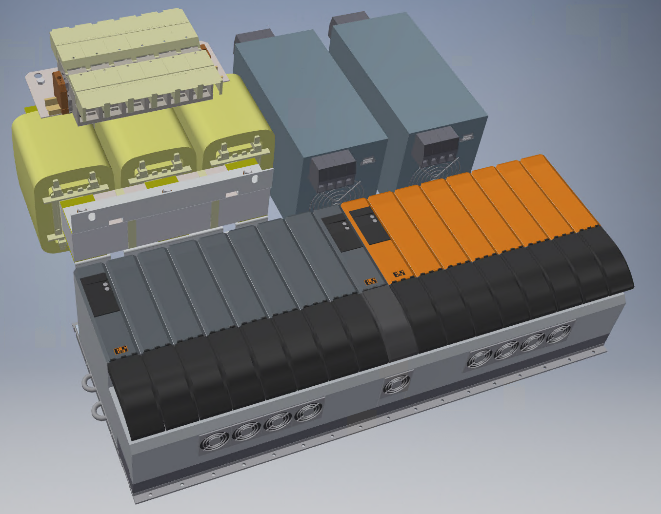
Turbine Control System Updates (Optional)
Tocardo already have a sophisticated turbine and platform control system. However, this assumes the power control system is easily accessible above water. Therefore, this control system needs to be updated to include the necessary feedback and control loops to manage faults and trigger automatic responses subsea to protect each turbine, the Subhub platform and the environment around it.
This request is optional and should be priced separately.
Assembly
The contractor will be responsible for procuring all the materials and parts and carrying out assembly onto a standardised cassette or framework which fits within the geometric constraints of the Subsea Power Control Units of the Subhub.
Commissioning
The contractor will wire up all the equipment in accordance with the specifications and commission all the equipment on the support frame.
Testing
A factory acceptance test will be setup to put each SPCU electronics system through its paces and demonstrate to QED that the system is fit for purpose. This testing will include measuring thermal signatures of the main equipment. It will also include connecting up the STXU to each SPCU.
Once acceptance is agreed the SPCU’s and STXU will be packaged up and sent to the integration yard (location to be agreed) to be connected to the new tidal turbines.
The Tocardo control software can run the generators in “motor” mode in order to test the system.
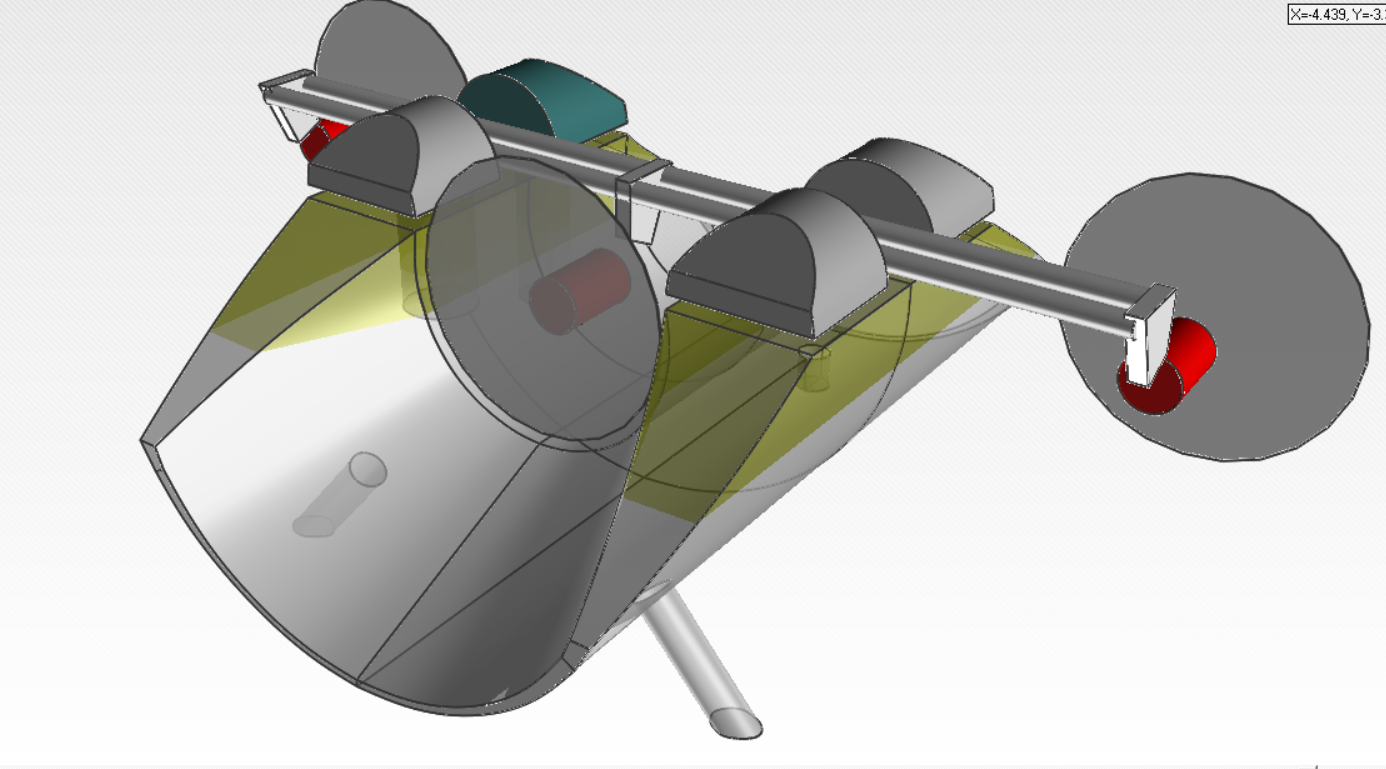
If you wish to apply or have any questions please email us at tenders@qednaval.co.uk and use the tender title above as the subject line.
Final Expression Of Interest (EOI) date 2nd April 2021
Final submission deadline: 12.00 B.S.T. 9th April 2021
Questions submitted:
Detailed Specification
Q1. The scope of work requires the contractor to design, develop and procure the materials to build a fully functioning SPCU – but there does not appear to be a detailed specification for this? Is this correct?
A1. There is an assumption made by ourselves that the invited tenders have experience in power electronics and understand the electrical components required to control the turbines and also control the grid side functions i.e. frequency matching and shut down if we lose the grid connection etc.
The 1st stage of the project is to provide QED with a list of the required components along with costs and thermal signatures. We refer to this as the functional specification. We can then look at the thermal loads in the cabinet and determine how much of a cooling issue we have. We will also check the geometric envelope fits within our Subsea Power Control Units (SPCU pressure hulls).
After the design review, we will need the contractor to purchase the components and start to assemble them onto the cassette provided, which slides into our SPCUs. They will then commission and test the system in the lab. Ideally this will include the implementation of the Tocardo control software onto the PLC controller.
Datasheet for the PMG
Q. 2 Would you be able to share the datasheet of the permanent magnet generator? As it will impact the control of the drives. For example, is the magnet surface mounted or embedded? What’s the back-EMF? We will need to consider solutions to consume the energy the PMG generated when losing the grid.
A.2 Yes, we will be able to share the data sheets once the tender has been awarded and under confidentiality clauses of the contract have been engaged. I will go back to the manufacturers now and ensure that we have ready access to this information.
Load Dump/Grid Connection (IMPORTANT INFORMATION)
Q3. It is understood that the community scale Subhub will initially export power generated to a simulated grid and electrical dump load mounted on a test barge moored within the test area. It appears the intention is for the dump load to be a relatively simple resistor bank and auxiliary power supplied by a diesel generator. A simple system like this is broadly possible, but only if the turbine inverters and control system were designed to facilitate it (similar to the design of an off-grid / islanded system) – The ITT for the SPCU however states that the designs should be “suitable for connection to national electrical grids in the UK and EU”, this would require a more sophisticated ‘grid simulator’ on the test barge.
A3. The (potential) issue in using a simple load dump is mainly around synchronisation with the grid, a grid tied inverter uses the grid as a voltage, frequency, and phase reference (essentially frequency matching as you say below). If you won’t have a grid connected to the back end of the inverter(s) then you either need an off-grid type inverter (which will generate its own voltage and frequency) or a system on the barge that emulates the grid. It would be easier and cheaper to use an off grid, or even a hybrid inverter, which would allow operation in both ‘modes’.
Pitch Controller and Braking
Q4A. Is there pitch control?
A4A. There is a patented, passive pitch control system called Bi-blade. It essentially balances the forces on both blades and takes up the required pitch. There is no requirement for the more traditional pitch controller. This is all controlled using Tocardo controllers.
Q4B. Is there a mechanical brake on the turbine/generator shaft?
There is a mechanical brake on the turbines and the associated electro-hydraulics (E-Box and H-Box) systems to operate the brake. It is a standard truck disc braking system so the parts are readily available. However, this does introduce a significant amount of complexity to the turbine and cost.
Q4C. Will we need a contactor to disconnect the PM generator from the converter?
The generator is connected to the converter using underwater, dry mate, electrical connectors. We would expect the system to be in the braked condition and the electricals to be disconnected or switched off if we are connecting/disconnecting these systems. In escence the QED Naval operations team would do the final integration under direction from the electrical contractor.
Q4D. Will we need electrical braking using a DC chopper and brake resistor or some form of high-speed electrical crowbar on the AC side?
A4D. At this stage electrical braking is only used up to the turbines rated condition. Brake resistors have been used in earlier Tocardo designs but these were for small generators. As I understand it, the larger the turbines the more difficult they become to use mechanical brake given there is so much torque. The braking systems are pretty complex to control and are obviously wear and tear items so we are considering the removal of the brakes in favour of electrical braking.
The most extreme design load, and the limit state of the turbine, is the “free spin mode”, where if we were operating the turbine beyond its rated condition and we were to lose the grid, then we have seconds to get the turbine under control i.e bring it under the rated condition so we can use electrical braking to stop it all together. Given current power control strategies and components, when operating beyond the rated condition, we need a mechanical means to stop the turbine.
Misclelaneous
Q5A. Outputs and Milestones – Does the technical approach suppose to be 60% and commercial approach 40% or vice versa?
A5A. The technical and commercial scores will be combined (Technical 60% / Commercial 40%) to determine the quotation which provides the most appropriate combination of quality and value for money.
Q5B. Is the SPCU subject to class requirement?
A5B. IEEE / IEC standards were more applicable for the power electronics. The Subhub platform applies DNV GL standards to drawings and plan approval so it is probably best to use those if applicable and for consistency.
Q5C. Environmental conditions – What are the required environmental temperatures for operation/transport/ storage?
A5C. This is a tenderers consideration and is set by the recommended guidelines of the components specified. The tenderer is expected to clearly state what parameters used in the design.
Q5D. System Interfaces – How is the internet connection provided? And, are interfaces to curtailment systems required (mammal detection?)
A5D. Access to the internet will be provided through a fibre channel link in the export cable to the installation barge. We have a backup RS484 interface with the Subsea Manifold (SM), which is directed connected to the Subhub on the seabed during operation but can easily be retrieved to the surface.
Q5E. HV Switch Gear – Is HV switch gear required?
A5E. Yes, this is required and stored in the STXU which contains the transformer but also Subhub’s Platform control system
Q5F. Connectors and Cabling – Who are the cable and connector suppliers?
A5F. Seacon MSSQ-4B connectors are currently used but this will be separately tendered.
Q5G. Electrical – External voltage is 3 phase/ 6.6kV (phase to phase)? What is the available short circuit current at the point of common coupling? Is a protection study required at the connection point? Which grid code is applicable for the site? Are there constraints on the energy storage medium? What is the required time of operation on battery
A5G. This is the current assumption but is subject to change. However, we are constrained by the space available within the STXU so 3-phase 6.6kVA was deemed to be a sensible limit.
Please see the connector specifications for this information which will be made available
Not required, unless IEC standards specify it, but seen as added value so please state clearly the benefits of such a study in the technical proposal
As stated previously. Initial sea trials will be connected to a load dump or more sophisticated grid simulator. However, ultimately this will be connected to UK/EU grid so suitable grid codes will be required and as such need to be specified clearly by the tenderer as part of their technical proposal.
The main constraint on energy storage is cost not space or weight. The Subhub platform has a massive payload capability.
Battery storage is optional since onboard turbine electrical supplies will be provided as parasitic power from the generator or drawn from the export cable. The battery storage is seen as a backup so between 3-6 hours low level power supply is required.
Q5H. We noticed on your website, it stated that “Final Expression of Interest date 2nd April 2021”, we want to confirm with you whether an official letter required, or [name’s] first email has qualified for it?
A5H. [Name] first email is sufficient for this purpose.
Visit our Seedrs page to invest in SUBHUB
Any questions?
We would love to hear from you.
Please don't hesitate to contact us if you have any questions about projects, our technology, or opportunities to work with us.
It has never been more important to make changes to our enrgy supply.
Our technology is ready to make a difference in the supply of sustainable renewable energy.